The first ”flight test” was in 2016, at The Irish Festival of Oulu in Finland - along with the trusty No. 1.
(–)
As expected, the old bellows is too small (5F) and a little leaky. And the ”wobbling” is somehow associated with the hand straps. They are thick enough, but they still feel wobbly.
(+)
The sound is good, but not great - with better bellows it will be really interesting. And it’s fairly light, even though there are 18 unused notes (= 36 reeds) inside...
Consairtín 2017, Ennis
I made new 7F bellows in January 2017. Much, much better. I also made the action a little ligther - now it sparkles! I had also added a couple of more notes in the top. Now I have the high C I “forgot” in No. 1...
The test
I brought both No. 1 and No. 3 (the WiMo) to Ireland. On the Thursday, my mate Richard Gammage and I stopped over in Feakle for the session in Shortt’s Bar. I started out on No. 1 and after a few tunes switched to No. 3. It was then Richard’s job to listen and point out the winner. After one set of tunes, he said: ”No discussion - it’s No. 3!” And so it has been, since then.
Mistakes?
Oh, yes, there are mistakes. For one, I forgot about the air button (or air lever), assuming that there would be room in the same location in the action as the original. No, there wasn’t. So the air lever ended up having a tunneled airway through the baseplate, under a lever. Very slow, but never mind - it’s not an Anglo.
With the bellows I made the mistake of tightening the final leather runs that go onto the ”peaks” of the bellows too much. It looks very good, but it has the effect that the bellows resists when closing completely. It is better today (Nov. 2018), but there is still some resistance and it’s a good reminder of the importance of effortless bellows movement. I “cooked” the bellows in the oven for 30 minutes at 50 °C, mounted in its compressor jig:
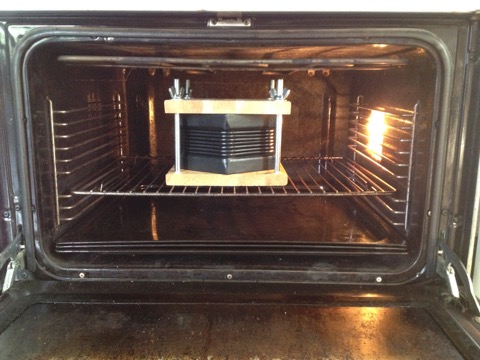
Shocking? No problem, as long as you lock the oven’s temperature dial with gaffa tape, just in case... It helped lot, but more is needed. I simply have to keep doing it and let the bellows cool in the compressor, assemble the instrument and place it in its case.
The wobbliness
When I returned from Ireland, I changed the hand strap fixture. I scrapped the ”wrap up over the frame” through an eyelet, and replaced it with the kind of fixture where the strap is clamped, close to the hand rest by a piece of bone, metal or wood (wood, in my case):
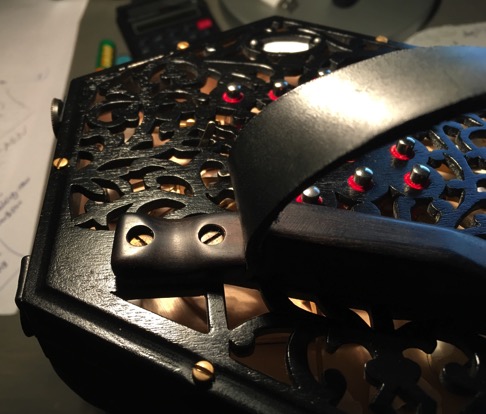
Oh, yes! That was better - the wobbliness is gone. Length is adjusted with a few holes in the other end of the strap, which held to the side of the hex frame by a screw and a brass brick; it’s primitive, but it works:
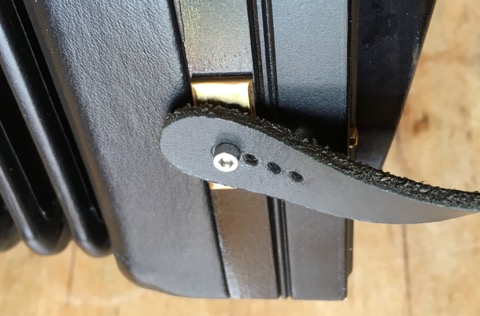
The thumb screw on top of the frame is now serving as holder for the right microphone lead. Microphones?! As if the damned thing isn’t loud enough...
The reason for microphones is not a question of volume, but a question of freedom to move about a little, and not be tied to a fixed position. It also ensures a dependable signal for the sound engineer’s desk.
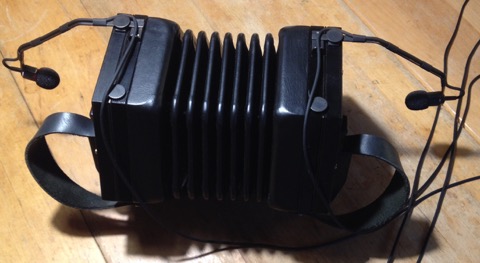
Next Previous